Precision woodworking machinery castings are a crucial component in the manufacturing of high-quality woodworking equipment. These castings are made from high-quality materials such as iron or steel and are carefully crafted to ensure the highest level of precision and durability. The process of creating precision woodworking machinery castings involves several steps. First, a mold is created using a pattern of the desired shape. This mold is then filled with molten metal, which is allowed to cool and solidify. Once the metal has hardened, the mold is removed, leaving behind a precise casting of the original pattern.
These castings are then machined and finished to the exact specifications required for the woodworking machinery they will be used in. This machining process is crucial in ensuring that the castings are perfectly smooth and free of any imperfections that could affect the performance of the machinery.
The precision of these castings is vital in the woodworking industry, as even the smallest imperfection can lead to a decrease in the quality of the finished product. By using high-quality materials and meticulous craftsmanship, manufacturers can ensure that their woodworking machinery will perform at the highest level and produce superior results.
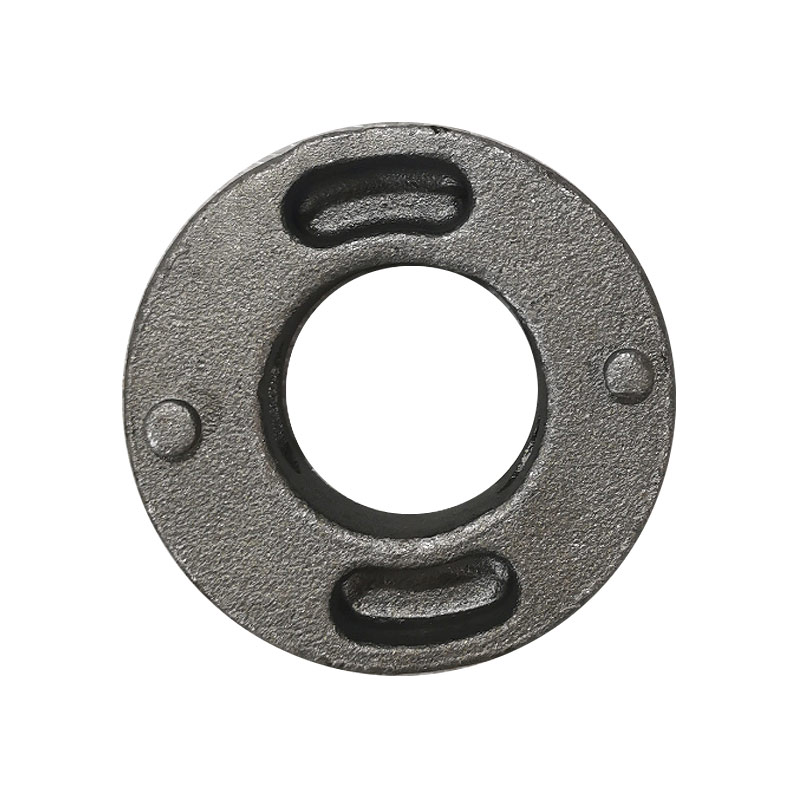
Name | Precision Die-Cast Barrier Arm Connector |
Material | ZG35 |
Process | Water Glass Investment Casting |
Weight | 0.75 Kg |
Product Standard | GB/T699-88 |
Features:
Customized production: OEM Fabricated Parts are usually customized according to the specific requirements and specifications of customers, which can meet specific functional and design needs.
Quality control: OEM manufacturers typically follow strict quality control standards to ensure the quality and consistency of finished parts.
Cost effectiveness: Through large-scale production and specialized division of labor, OEM can reduce production costs and provide customers with affordable solutions.
Technical expertise: OEM manufacturers often have deep technical accumulation and professional knowledge in specific fields, and are able to produce technically complex parts.
Flexibility and adaptability: OEM manufacturers can quickly adapt to market changes and customer needs, and flexibly adjust their production lines.
Mass production capability: OEM manufacturers have the ability to produce on a large scale and meet the needs of large orders.
Brand neutrality: OEM finished parts are usually brand neutral, allowing customers to sell these products under their own brand names.
Innovation capability: Many OEM manufacturers continuously invest in research and development to provide innovative finished component solutions.
Delivery time guarantee: OEM manufacturers are usually able to provide fast delivery services to meet customers' urgent needs.
After sales service support: Some OEM manufacturers provide after-sales service support, including product maintenance, repair, and replacement.
Applications
Automotive industry: OEM is widely used in the automotive industry, and many car manufacturers place their brands on cars, but in reality, they are produced by OEM manufacturers.
In the field of electronic products, electronic products such as mobile phones, computers, and cameras can be produced through OEM to meet market demand.
Home appliance industry: Home appliances are also one of the main application areas of OEM, and many brand companies entrust product design and marketing to OEM manufacturers.
Medical equipment: In the field of medical equipment, OEM manufacturers produce products that ensure quality and performance, meeting high industry standards.
Aerospace: The aerospace industry also requires OEM manufacturers to provide high-quality parts and components.
Mechanical equipment: The mechanical equipment industry has high requirements for product quality and technology. By cooperating with professional OEM manufacturers, we ensure the quality and performance of our products.
Electronic equipment manufacturing industry: The electronic equipment manufacturing industry is also a part of the OEM market, including HVAC, electronic equipment manufacturing, etc.
Wind and solar power: The new energy sector, such as wind and solar power, also involves OEM applications.
Construction Machinery: The construction machinery industry is also a part of the OEM market.
FAQ:
What materials are used in the manufacturing of the Precision Die-Cast Barrier Arm Connector?
During the process of making this piece, water glass precision casing technology is used using good materials only.
Can the Die-Cast Barrier Arm Connector be customized according to specific requirements?
Yes, we manufacture this item after analyzing client drawings such that it meets exact specifications or wants of an individual buyer.
What industries commonly use this Die-Cast Barrier Arm Connector?
This item finds more applications within the access controls industry as well as many security gates systems specifically within these barrier systems that they deploy there.
How does the die-casting process benefit the product?
It results into products which are accurate; their consistency also makes them last long while performing efficiently within their intended use.
DONGRON is passionate about the provision of high-quality machining and precision casting products. The manufacturing of our Precision Die-Cast Barrier Arm Connector exemplifies our commitment to excellence and innovation in manufacturing. Contact us now for more information about our products and how we can help you with your specific needs.