Woodworking Machine Casting Parts are important components in woodworking equipment, responsible for providing stability, durability, and accuracy in the execution of various woodworking tasks. These parts are carefully designed and manufactured using high-quality materials and advanced casting techniques to ensure optimal functionality and lifespan. The process of casting woodworking machinery parts involves pouring molten metal into molds that correspond to the required shape and size of the parts. This method can accurately achieve complex designs and shapes. The use of advanced casting technology and equipment enables manufacturers to produce high-quality parts that meet specific requirements for woodworking machinery. A key advantage of using Woodworking Machine Casting Parts is their excellent strength and durability. Castings can withstand heavy loads, high temperatures, and harsh working conditions without compromising their structural integrity. This ensures that woodworking machines can operate efficiently and effectively throughout their entire service life, with excellent precision and accuracy in addition to strength and durability. The precise dimensions and complex design of castings enable woodworking machines to operate with high precision, consistency, and repeatability. This enables high-quality woodworking products to meet customers' exact specifications and requirements.
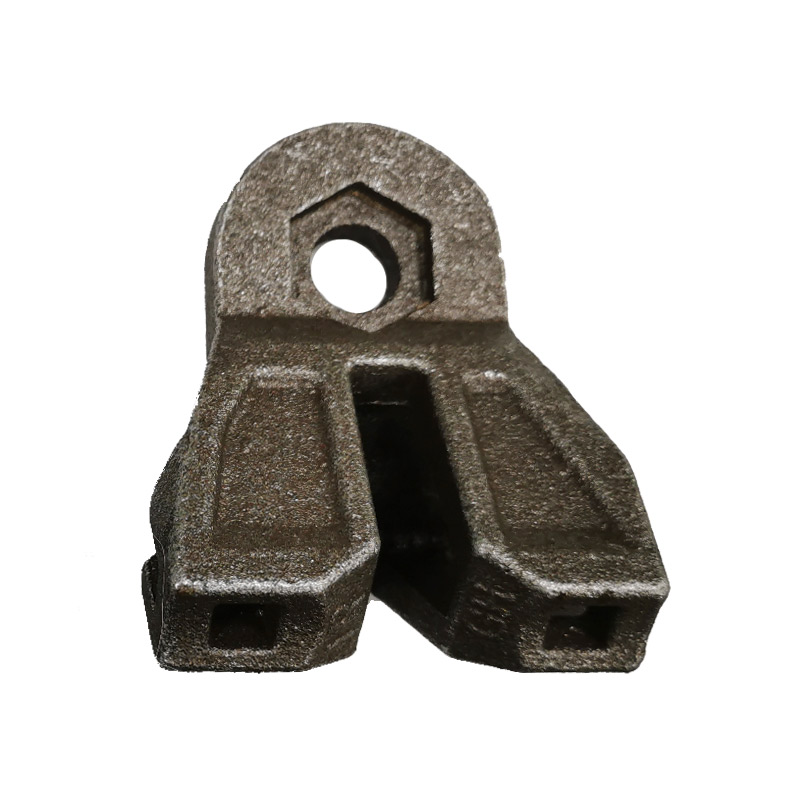
Name | Precision Die-Cast Barrier Arm Connector |
Material | ZG35 |
Process | Water Glass Investment Casting |
Weight | 0.75 Kg |
Product Standard | GB/T699-88 |
Features:
Complex geometric shapes: Customized wood working machine casting components can produce parts with complex geometric shapes, which may be difficult to achieve in traditional mechanical processing.
Cost effectiveness: For mass production, custom wood working machine casting components can provide cost-effectiveness as it reduces material waste and improves production efficiency.
High strength and durability: These components typically have high strength and durability, making them suitable for applications that require withstanding heavy loads and harsh working environments.
Precision manufacturing capability: Customized wood working machine casting components can achieve precise machining tolerances, allowing for an accuracy of 0.3-1.5 mm.
Diversified material selection: Different alloy materials can be selected according to application needs, such as AL360, AL380, AL383, AL413, ZA-8, ZA-12, ZA-27, aluminum A356, etc.
Surface treatment capability: Customized wood working machine casting components can undergo various surface treatments, such as sandblasting, shot blasting, polishing, anodizing, oxidation, electrophoresis, chromate, powder coating, and spray painting.
Multiple manufacturing processes: including die-casting, mold manufacturing, CNC milling, CNC turning, CNC drilling, and other manufacturing processes.
Quality assurance: Strict quality control and multiple ISO certifications ensure the high quality standards of the products during the production process of customized wooden work machine casting components.
Applications
Automotive industry: Customized wood working machine casting components have a wide range of applications in the automotive industry, such as key components such as the turbocharger turbine, cover plate, and liner.
Aerospace industry: In the aerospace field, these components can be used to manufacture guide vanes and rotating blades, impeller blades, heat shields, etc., to meet the requirements of lightweight design and high durability.
The energy industry, including oil and gas, hydropower, coal-fired power, renewable energy generation, and nuclear power, plays an important role in the production of customized wooden work machine castings.
General mechanical components: including shaft parts (such as stepped shafts, electric spindles, camshafts), housing parts (such as spindle boxes, gearboxes, engine cases), disc parts (such as bearing covers, pulleys), threaded parts (such as sliding screws), and gear parts (such as spur and cylindrical gears).
FAQ:
What materials are used in the manufacturing of the Precision Die-Cast Barrier Arm Connector?
During the process of making this piece, water glass precision casing technology is used using good materials only.
Can the Die-Cast Barrier Arm Connector be customized according to specific requirements?
Yes, we manufacture this item after analyzing client drawings such that it meets exact specifications or wants of an individual buyer.
What industries commonly use this Die-Cast Barrier Arm Connector?
This item finds more applications within the access controls industry as well as many security gates systems specifically within these barrier systems that they deploy there.
How does the die-casting process benefit the product?
It results into products which are accurate; their consistency also makes them last long while performing efficiently within their intended use.
DONGRON is passionate about the provision of high-quality machining and precision casting products. The manufacturing of our Precision Die-Cast Barrier Arm Connector exemplifies our commitment to excellence and innovation in manufacturing. Contact us now for more information about our products and how we can help you with your specific needs.