The pump casing is a crucial component of a pump that houses the impeller and other internal parts. It plays a vital role in containing the pumped fluid and directing it towards the discharge outlet. pump casing parts are designed to withstand high pressures, temperatures, and corrosive environments to ensure efficient and reliable pump operation.
One of the key pump casing parts is the volute casing, which is a curved, funnel-shaped casing that surrounds the impeller. Its primary function is to collect the liquid discharged from the impeller and convert the kinetic energy into pressure. The volute casing is designed to minimize turbulence and energy losses, thereby improving the pump's efficiency.
Another important pump casing part is the suction casing, which is located at the inlet of the pump. Its purpose is to guide the fluid into the pump and ensure a smooth flow towards the impeller. The suction casing is designed with a larger diameter than the impeller to reduce the velocity of the incoming fluid and prevent cavitation, which can damage the pump components.
The casing wear rings are also essential pump casing parts that help reduce leakage and improve pump efficiency. These wear rings are installed on the impeller and casing to minimize the clearance between them, which helps maintain optimal pump performance. They are typically made of materials that are resistant to wear and corrosion, such as bronze or stainless steel.
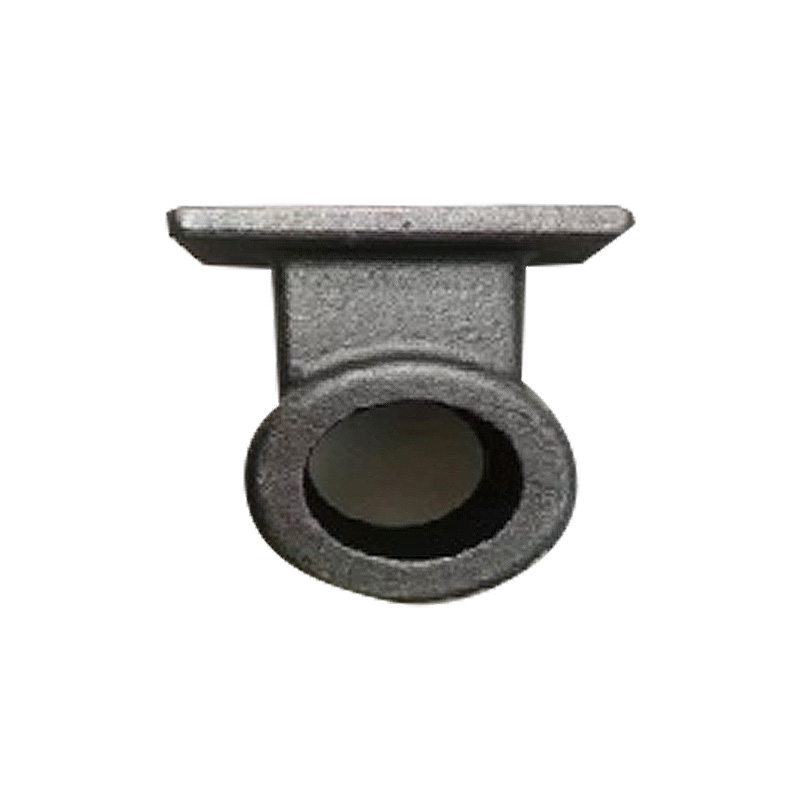
Applications:
Industrial and urban water supply and drainage: used for boosting water supply in high-rise buildings, garden irrigation, fire boosting, long-distance transportation, etc.
Chemical industry: In chemical production, pump casings are used to transport corrosive liquids and require corrosion-resistant materials.
Pharmaceutical and medical industries: Due to the need for strong corrosion protection, pump casings are used in the pharmaceutical and medical industries to transport drugs and medical waste.
Sewage treatment plant: The pump casing is used for pumps in sewage treatment plants to cope with corrosive and abrasive media.
Paper industry: In the paper industry, pump casings are used to transport media such as pulp.
Heat exchange and cooling system: The pump casing is used to transport hot fluids in systems that require temperature control, such as heat exchangers and cooling systems.
Power plants and general industrial power plants: Pump casings are used for transporting condensate water from power plants and general industrial power plants.
Oil and gas: In the oil and gas industry, pump casings are used to transport high-pressure fluids.
Features:
Sealing: The main function of the pump casing is to seal the inside of the pump, prevent leakage, and maintain pressure.
Structural diversity: The pump casing can have different structures according to the type of pump, such as volute pumps, barrel pumps, elbow pumps, etc.
Material selection: The pump casing can be made of metal, solid plastic, plastic lining, and ceramic lining. Metal pump casings are usually made of stainless steel, duplex alloys, nickel and nickel based alloys, titanium and titanium alloys, etc.
Pressure resistance: When designing the pump casing, the pressure range needs to be considered. For high-pressure pumps, the wall thickness of the pump casing needs to be increased to withstand pressure.
Split design: For ease of installation, the pump casing may need to be divided radially or axially.
Bearing support: The pump casing sometimes includes bearing brackets to support the cantilever pump shaft.
Sealing method: Pump casing components are usually sealed against internal pressure through gaskets, O-rings, or direct metal to metal sealing.
Heat exchange design: The pump casing may include a heat barrier and a cooling shell to reduce the heat flow from the inside of the pump to the pump bearings and shaft seals.
Manufacturing method: The pump casing can be cast, forged, welded, pressed, or stretched.
Parameter:
Name | Precision Die Cast Base Cover Connection Plate |
Material | ZG35 |
Process | Water Glass Investment Casting |
Weight | 0.8 Kg |
Product Standard | GB/T699-88 |
FAQ:
What materials are used in the manufacturing of the Precision Die-Cast Base Cover Connection Plate?
The use of water glass precision casting process ensures that we make these base cover connection plates from superior materials.
Can the base cover connection plate be customized according to specific requirements?
Yes, we create this product depending on our clients’ drawings so as to conform to their specific needs and preferences.
What industries commonly use this base cover connection plate?
This component has found wide usage in hydraulic cylinder industry and also material handling equipment’s interconnection systems.
How does the die-casting process benefit the product?
Die-casting makes this product reliable because of its consistency, durability, high-precision levels suitable for its intended purposes in terms of design performance, etc., if well-defined goals are met during fabrication stages or due course of its use.
DONGRON is a leading manufacturer in machining and precision casting. Our dedication to manufacturing excellence and innovation is exemplified by our Precision Die-Cast Base Cover Connection Plate. Talk to us for more information about our products and how we can help you meet your specific requirements.