Steel forged vehicle components castings are necessary elements in the car industry, offering strength, durability, and precision for a number of car applications. These castings are produced the usage of the metal casting process, which entails melting metal in a furnace and pouring it into a mould to create the preferred shape.One of the key benefits of metal forged car components castings is their highest quality electricity and durability. Steel is recognized for its excessive tensile electricity and affect resistance, making it an best cloth for integral automobile factors such as engine blocks, transmission housings, and suspension components. Steel castings can face up to excessive stages of stress and vibration, making sure dependable overall performance underneath stressful running conditions.
In addition to strength, metal solid vehicle components castings provide brilliant dimensional accuracy and consistency. The casting manner approves for complicated shapes and difficult designs to be accomplished with precision, making sure a ideal in shape and alignment in the ultimate assembly. This degree of accuracy is vital for keeping the overall performance and protection of the vehicle, as even minor deviations can lead to operational troubles or failure.
Furthermore, metal forged vehicle components castings can be produced in a low in cost manner, making them a aggressive preference for car manufacturers. Steel is a extensively reachable and incredibly less expensive material, and the casting procedure approves for environment friendly manufacturing with minimal waste. This consequences in decrease manufacturing charges and shorter lead instances in contrast to different manufacturing methods, making metal castings a sensible answer for high-volume production.
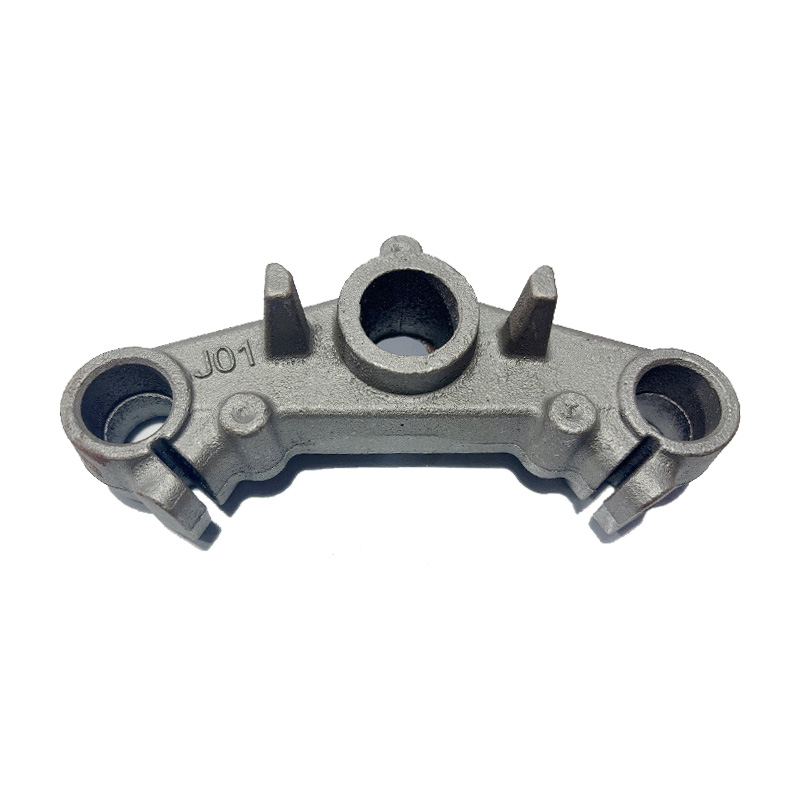
Applications
Chassis components: which includes suspension system, steerage system, braking system, etc. These factors want to stand up to enormous forces and influences for the duration of use, consequently requiring excessive sturdiness and strength.
Wheels: Wheels manufactured via casting science no longer solely have properly energy and durability, however additionally minimize the weight of the wheels, enhance the gas economic system and coping with overall performance of the car.
Engine components, such as engine mounts, have excessive mechanical overall performance necessities due to the heavy weight of the engine itself and the robust vibrations it generates at some point of operation.
Transmission machine components, such as driveshafts, are mechanical components used to transmit torque and rotation between the engine and wheels of a vehicle.
Vehicle structural components: such as built-in axle shells, used to substitute welded axle shells and new merchandise with semi axle sleeve forged axle shells, attaining built-in casting of castings.
Safety gadget components, such as collision avoidance structures and related elements of airbags, want to meet excessive security requirements such as NCAP.
Features;
High energy and durability: Steel forged components, due to their cloth properties, can grant the required electricity and sturdiness to stand up to more than a few masses for the duration of automobile operation.
Lightweight: While making sure the power and protection overall performance of the car, metal castings are optimized to acquire light-weight design, enhance the energy overall performance of the car, decrease gasoline consumption, and decrease exhaust pollution.
Integrated design: Through built-in design, more than one components are merged into one casting, decreasing processing issue and fee whilst enhancing structural stress and reliability.
High precision and complicated shapes: Steel castings can manufacture aspects with excessive precision and complicated shapes, assembly the precision and format necessities of cutting-edge automobiles.
Environmental adaptability: Steel forged elements have exact corrosion resistance and warmness resistance, and can adapt to more than a few environmental conditions.
Cost effectiveness: Through casting technology, large-scale manufacturing can be achieved, lowering the value of character aspects and enhancing manufacturing efficiency.
Parameter;
Name | Precision Die Cast Tailgate Arm |
Material | ZG35 |
Process | Water Glass Investment Casting |
Weight | 4.8 Kg |
Product Standard | GB/T699-88 |
FAQ:
What are the materials used in producing Precision Die Cast Tailgate Arm?
The process of water glass precision casting enabled us to use quality materials when making this kind of arm for tailgate.
Can I have a customised Precision Die Cast Tailgate Arm made as per my specifications?
Yes, since it is manufactured as per drawings from customers thus meeting their exact requirements.
Which industries commonly utilize this type of Precision Die Cast Tailgate Arm?
This type of one is typically used in trucks and heavy duty vehicles with specific applications to their respective tails gate systems.
How does the die casting help this product?
Die casting enables us to achieve high precisions, consistencies, durabilities hence making it more dependable while running efficiently in its intended working environment
DONGRON is dedicated to offering high quality machining and precision casting products. Such dedication towards excellence and innovation in manufacturing is exemplified by our Precision Die Cast Tailgate Arm. If you have any inquiries regarding our products or want us to meet your specific needs, please contact us today.