Customization is the key to ensuring the highest quality and performance when manufacturing automotive castings. Customization allows for meeting precise specifications, resulting in parts tailored to specific needs of the vehicle and its intended use.
automotive castings are essential components in automotive production, as they provide structural support and functionality for various systems inside the car. These parts must be durable, reliable, and able to withstand the strict requirements of daily use.
By customizing automotive castings, manufacturers can ensure that each component meets the exact requirements of the vehicle. This includes considerations such as material selection, design specifications, and manufacturing processes. Customization can also improve the performance, efficiency, and overall quality of parts.
A key benefit of customizing automotive castings is the ability to optimize the design for specific functions and applications. This can make the parts lighter, stronger, and more efficient, thereby improving fuel economy, reducing emissions, and enhancing overall performance.
Customization allows for greater flexibility in the production process, enabling manufacturers to meet tight deadlines and production schedules. By customizing automotive castings, manufacturers can also reduce waste, lower costs, and improve the overall efficiency of the manufacturing process.
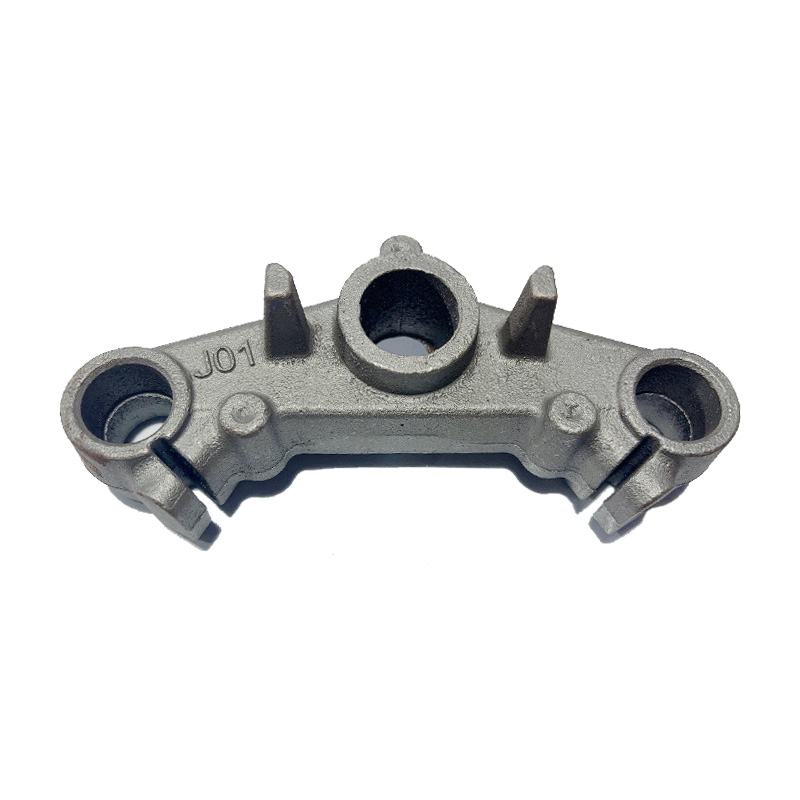
Applications
Engine components: such as cylinder heads and gas engine parts, as well as mounting brackets for electric motors and stepper motors.
Transmission and chassis components: including electronic housings for gearboxes, motors, sunshades, etc., as well as transmission and chassis components.
Safety system: sensors and airbag housings as active safety mechanisms, as well as seat belt winding spools.
Fuel system: fuel intake components, as well as air conditioning system.
Electronic equipment: shielding telematics and electronic equipment, including connectors and sensors for autonomous vehicle.
Power steering and braking system: Durable power steering and braking system.
Body structure: such as the ultra hard 30X cold-rolled stainless steel alloy used in Tesla Cybertruck, used in body manufacturing to provide durability and aesthetics.
Turbine blades and exhaust manifolds: Cast steel automotive components such as turbine blades and exhaust manifolds are precision manufactured through investment casting to optimize performance.
Brake system components: including brake calipers, brake discs, and brake pads, ensuring high precision, reliability, and durability through investment casting.
Features;
Precision casting capability: Customized automotive casting components can cast various complex and precise parts, such as pistons, cylinders, exhaust manifolds, etc. These products have the characteristics of complex shapes, high dimensional accuracy, and good surface smoothness.
High strength and durability: Automotive die-casting parts help produce complex shaped parts with high durability and improved aesthetic appearance.
Material diversity: Different materials can be selected according to different performance requirements, such as aluminum, magnesium alloys, and titanium alloys, to meet the requirements of lightweight, strength, and corrosion resistance.
High production efficiency: Customized cast parts are suitable for large-scale production, capable of producing a large number of parts in a short period of time with high precision.
Lightweight: Using lightweight materials such as aluminum and magnesium alloys can help reduce the weight of cars, improve fuel efficiency and performance.
Design flexibility: Casting processes can produce parts with complex shapes, which may be more difficult or expensive to manufacture using other methods.
Cost effectiveness: Casting is a relatively economical manufacturing process suitable for large-scale production, and the best materials can be selected based on the required strength, weight, and corrosion resistance.
High precision and tolerance: Casting can produce parts with high precision and dimensional tolerance, as the mold is precisely machined to the desired shape.
Die Casting Automotive Parts Parameter
Name | Precision Die Cast Tailgate Arm |
Material | ZG35 |
Process | Water Glass Investment Casting |
Weight | 4.8 Kg |
Product Standard | GB/T699-88 |
FAQ:
What are the materials used in producing Precision Die Cast Tailgate Arm?
The process of water glass precision casting enabled us to use quality materials when making this kind of arm for tailgate.
Can I have a customised Precision Die Cast Tailgate Arm made as per my specifications?
Yes, since it is manufactured as per drawings from customers thus meeting their exact requirements.
Which industries commonly utilize this type of Precision Die Cast Tailgate Arm?
This type of one is typically used in trucks and heavy duty vehicles with specific applications to their respective tails gate systems.
How does the die casting help this product?
Die casting enables us to achieve high precisions, consistencies, durabilities hence making it more dependable while running efficiently in its intended working environment
DONGRON is dedicated to offering high quality machining and precision casting products. Such dedication towards excellence and innovation in manufacturing is exemplified by our Precision Die Cast Tailgate Arm. If you have any inquiries regarding our products or want us to meet your specific needs, please contact us today.